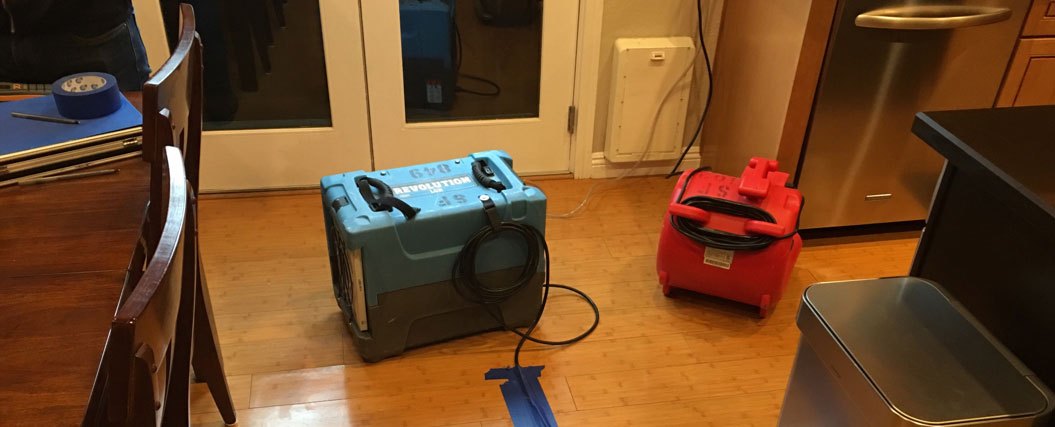
If you’ve experienced any sort of flooding in your home or business, is it enough to pump or drain away standing water then mop up? No, that’s only the beginning of mitigating against mold, decay, warping, buckling, and other water damage.
How about using a wet vac to extract dampness from carpet and building surfaces?
Only if just a part of a single room is affected, and there wasn’t time for water to thoroughly soak the area. Otherwise, it’s likely that enough water has soaked through flooring and into the concrete or wood sub-floor. It may even be creeping upwards inside walls. Once there, it can take weeks to evaporate. All during that time, it’s causing progressive damage
Without rapid structural drying to remove deeply trapped moisture, you’re likely to end up with a lot of damage that could have been prevented with immediate action.
So precisely what is structural drying?
Properly done, it’s using state-of-the-art procedures and equipment to remove all excess moisture, no matter how deeply it’s traveled, in just a couple of days.
As you might expect, the first step is water removal by pumping, draining, mopping, and so on. Then comes water extraction using powerful specially-designed vacuum equipment. Preparation also includes removing damp items such as clothes and furniture, along with any unsalvageable building materials. That lessens the task of what we consider the two steps of structural drying proper.
Air Movement
It’s all about promoting evaporation. And that means lots of air movement to take away the water vapor that soon fills the air. Doing that right involves using powerful high-volume axial fans and centrifugal air movers.
Ideally, this is non-invasive. That is, without altering the building. Building dry-out used to mean always lifting or even removing carpet, but that isn’t always necessary now days. That said, it’s sometimes necessary. It may also be necessary to remove baseboard and crown molding and make a series of small holes in order to dry structural framing quickly enough. Blowers designed for the higher air pressures then send in dryer air, forcing moist air out. The holes are later covered by replacing the baseboard and molding. But in extreme cases, it may be necessary to remove flooring, wallboards, and ceiling materials.
Dehumidification
Indoor relative humidity needs to be kept low to draw water vapor out from deep within the structure. And failing to control humidity can lead to mold and other problems in areas that weren’t harmed by the original flooding.
Professionals use industrial high-volume refrigerant dehumidifiers specifically designed for water damage mitigation. They condense water vapor out of the air by the gallon. Besides RH (relative humidity) moisture in the air can also be expressed in grains (a unit of weight) of water per pound of air. So especially effective equipment is referred to as LGR — low-grain refrigerant dehumidifiers. Advanced designs are necessary to work properly at temperature extremes. But it’s best to keep temperatures between 70 and 90 degrees whenever possible. That’s a balance between rapid evaporation and not encouraging bacteria and mold growth. For small areas, silica gel desiccants can be used instead.
Frequent measurements and adjustments are critical in keeping everything moving as rapidly as possible, as well as in determining that there’s negligible excess moisture left to remove. And there’s such a thing as drying the building too quickly, as this can damage hardwood floors and other woodwork. Besides measuring indoor air humidity, the moisture content of various building materials should be measured as well. In some situations, thermal imaging to spot damp cooler areas, as well as bore-scopes to peer inside building cavities, can provide helpful information.